Featured Articles
Latest Articles
Proven Results Across Industries
See how successful brands like yours drive post-purchase customer experience with ClickPost.
ClickPost's integration feature allows for swift carrier integrations, enabling a one-point contact for seamless collaboration with multiple carriers.
Read case studyClickPost's automated NDR module helps you address non-delivery concerns, ensuring swift resolution for enhanced customer satisfaction.
Read case studyClickPost provides real-time alerts on order movement, complete control over carriers, and automated resolutions for B2B logistics.
Read case studyClickPost's automated logistics solutions resolve shipment delays, improve on-time deliveries, & provide real-time order visibility.
Read case studyClickPost's Revolutionary EDD Module helps you make accurate Delivery Predictions for Enhanced Customer Trust.
Read case studyRecent Mentions
Urban congestion to remote delivery: Tackling India’s logistics puzzle.
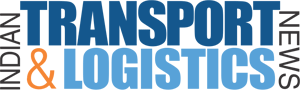
Berrylush Partners with ClickPost to Drive Customer Retention to 35% in 2025
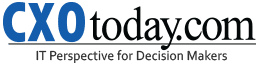
Breaking Down Barriers - Why Omnichannel is the Future of Retail
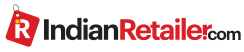
Tier-II and Tier-III cities fuel festive season sales: ClickPost report

The Link Between Intelligent Shipping Automation & Profitability
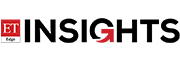
How e-commerce is revitalising India’s handloom heritage
Image Business of Fashion
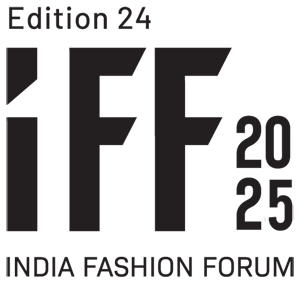
Get the Latest Shipping News, Expert Guides and Invites.
From ClickPost Video Library
- All
- eCommerce
- Featured
- Shipping
- Shopify
- Carrier
- Logistics
- Courier
- comparison
- Returns
- Supply chain
- Delivery Management
- Last Mile
- eCommerce Companies
- Label
- Alternatives
- EDD
- Fulfillment
- Hyperlocal
- Glossary
- Inventory
- Calculator
- Customer Experience
- Dropshipping
- Engineering
- Logistics Companies
- Narvar
- Shipment Tracking
- Shipping Carriers US
- Thought Leadership
- eCommerce Fulfillment
- quick commerce
