Table of Contents
What is Automated Shipping? How shipping automation works? What are its benefits?
Introduction
Efficient shipping systems are no longer an operational need in the ever-evolving digital era. They are a strategic advantage. With eCommerce sales projected to surpass USD 8 trillion by 2027, businesses are scaling rapidly, handling more customers and orders than ever before. Amid this growth, automated shipping has emerged as a transformative solution. It simplifies logistics and ensures faster and error-free delivery processes.
Automation in logistics is no longer a luxury reserved for large enterprises; it is becoming essential for businesses of all sizes. By integrating technology with traditional processes, automated shipping solutions enable businesses to meet rising consumer expectations while reducing costs and increasing efficiency.
Here are some key trends driving the adoption of automated shipping systems:
Key Trends
-
Rapid Growth in Online Sales: The surge in eCommerce has created a need for scalable shipping solutions to manage higher order volumes.
-
Cost Optimisation: Automated shipping reduces manual intervention. It minimizes errors and operational costs.
-
Technological Advancements: AI, machine learning, and IoT are making shipping automation more accessible and effective than ever.
-
Customer Expectations: Fast and accurate deliveries have become a baseline expectation for modern consumers.
What is Automated Shipping?
Automated shipping refers to the integration of software and hardware systems that simplify and refine shipping processes. From receiving an order to delivering it at the customer’s doorstep, automation eliminates manual intervention at various stages. As a result, it improves speed, accuracy, and scalability while reducing shipping costs.
For eCommerce businesses, automated shipping is way beyond just operational convenience. It is now a necessity to stay competitive. By automating tasks like order processing, label generation, and real-time tracking, businesses can refine workflows, focus on growth, and deliver a superior customer experience.
Key characteristics of automated shipping include:
-
Streamlined Workflows: Orders are queued and processed automatically, reducing manual errors.
-
Improved Speed: Automation ensures quicker transitions between order receipt, processing, and dispatch.
-
Scalability: Automated systems can handle high volumes without compromising efficiency.
-
Improved Customer Experience: Real-time tracking and accurate delivery timelines improve overall customer experience.
How Automated Shipping Works?
Automated shipping systems combine software and hardware to simplify logistics operations. These systems work seamlessly to ensure orders are processed efficiently, packages are prepared accurately, and deliveries are tracked in real time. Below is how automated shipping works:
Below is how automated shipping works:
-
Order Integration: Orders are automatically imported from eCommerce platforms into the shipping software. It eliminates the need for manual data entry. Hence, it reduces errors and saves time.
-
Inventory Coordination: The software integrates with inventory management systems to check stock availability and allocate products for dispatch. It ensures the correct items are picked, avoiding delays.
-
Label Generation: The system generates shipping labels, barcodes, and tracking numbers based on the order details. The automatic printing and application of these labels expedite the packaging process.
-
Carrier Selection: Automatic shipping systems select the most cost-effective and efficient carrier for each shipment. It considers criteria like delivery timelines, destination, and package weight.
-
Package Dispatch: Packages are transported to local carriers or hubs using predefined workflows. In large-scale setups, this stage may involve conveyor belts or automated loaders.
-
Real-Time Tracking: Customers receive tracking links to monitor their package's progress. Businesses also use this feature to ensure on-time deliveries and proactively address delays.
-
Delivery Confirmation: Once the package is delivered, the system updates the order status automatically and notifies both the customer and the business.
Key Features of Automated Shipping Solutions
Automation in shipping introduces innovative features that ease the processes and also improve efficiency and customer satisfaction.
Below are some key features:
1. Integration with E-Commerce Platforms
Automated shipping solutions easily connect with popular e-commerce platforms like Shopify, WooCommerce, and Amazon. This eCommerce API integration enables businesses to handle all shipping-related tasks directly from their online store dashboards.
Key Benefits:
-
Order Importation: Orders are synced automatically, eliminating manual data entry.
-
Centralized Operations: Manage multiple sales channels from a single platform.
-
Live Updates: Tracking information is instantly updated, keeping both businesses and customers informed.
2. Label Generation and Carrier Selection
Shipping automation simplifies label creation and refines carrier selection. As a result, it ensures cost-effective and efficient deliveries.
Key Benefits:
-
Quick Label Creation: Automatically generate accurate shipping labels with essential details.
-
Smart Carrier Selection: Evaluate carriers based on delivery time, costs, and destination suitability.
-
Error Reduction: Avoid manual mistakes in label generation and carrier assignments.
3. Real-Time Tracking
Real-time tracking provides complete visibility over shipments. That ensures transparency and efficiency throughout the delivery process.
Key Benefits:
-
Customer Experience: Customers can monitor the progress of their orders, reducing uncertainty.
-
Operational Insights: Businesses can identify delays and resolve them promptly.
-
Improved Trust: Accurate tracking builds confidence among consumers.
4. Returns Management
Returns are an inevitable part of logistics. Implementing automated shipping refines reverse logistics to save time and effort.
Key Benefits:
-
Easy Return Labels: Generate return shipping labels automatically.
-
Easy Coordination: Track return shipments and manage refunds or exchanges.
-
Insightful Data: Analyse return patterns to refine inventory and minimize future returns.
Top 10 Automated Shipping Software Platforms
Automated shipping software platforms are the backbone of modern logistics. They help businesses improve their shipping processes. Below is a detailed breakdown of the top 10 platforms revolutionizing the shipping landscape.
Platform | Description |
---|---|
ClickPost | Comprehensive platform offering multi-carrier integration, tracking, returns management, and COD reconciliation. |
ShipStation | SaaS-based tool centralizing shipping tasks, with features like label generation and order splitting. |
AfterShip | Offers real-time tracking, multi-carrier support, and warranty automation for better delivery efficiency. |
ShipBob | A 3PL platform automating order fulfillment with robust warehouse management tools. |
Shippo | Focuses on multi-carrier integration, discounted rates, and end-to-end workflow automation. |
ShippingEasy | Provides automated rules, inventory management, and carrier rate comparisons for improved shipping. |
Easyship | Aggregates 250+ shipping solutions, automating courier selection and customs documentation. |
Veeqo | Free platform offering bulk shipping, real-time tracking, and immediate rate discounts. |
ShipHero | Combines warehouse management with AI-powered shipping automation and efficient routing. |
SendCloud | Automates shipping and returns processes with advanced tools for faster and error-free operations. |
1. ClickPost
ClickPost stands out as a comprehensive logistics management platform tailored for eCommerce businesses. Its advanced features include automated order creation, label generation, and multi-carrier integration. The platform excels in handling delivery exceptions, with an EDD (expected date of delivery) prediction tool that uses real-time data to calculate timelines. ClickPost also offers modules for shipment tracking, returns management, and COD reconciliation. These features make it a preferred choice for businesses aiming to improve their post-purchase experience.
Streamline your shipping experience with ClickPost
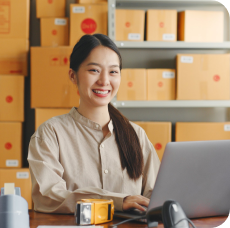
2. ShipStation
ShipStation is a SaaS-based platform that centralizes shipping tasks for businesses. Its standout features include the ability to import orders from over 40 sales channels, generate shipping labels, and validate shipping addresses. With advanced inventory management and the capability to split or merge orders, ShipStation provides flexibility and control. Its integration with major carriers and platforms ensures free-flowing operations. At the same time, its tiered pricing plans cater to businesses of all sizes.
3. AfterShip
AfterShip offers a robust suite of automated solutions for eCommerce companies. Known for its tracking capabilities, it connects with over 1,000 global carriers to provide real-time shipment updates. AfterShip’s automated tools include shipping label generation, shipping rate comparisons, and warranty management. Its multi-carrier support and ability to integrate with existing tech stacks make it a versatile choice for enhancing delivery efficiency.
4. ShipBob
ShipBob is a 3PL platform that automates the entire order fulfillment process. When integrated with an online store, it handles picking, packing, and shipping tasks. ShipBob’s proprietary warehouse management system provides real-time metrics, while its barcode scanning technology ensures accuracy. The platform also excels in supply chain optimization. That makes it a valuable partner for growing eCommerce businesses.
5. Shippo
Shippo focuses on automating workflows for businesses of all sizes. Its multi-carrier integration supports platforms like UPS, FedEx, and USPS, enabling easy rate comparisons and label generation. Shippo’s ability to scale with a business, coupled with its discounted carrier rates, makes it a cost-effective solution for automating logistics operations.
6. ShippingEasy
ShippingEasy is known for its automation tools that simplify order fulfillment. Its standout features include automated shipping rules, inventory management across multiple platforms, and carrier rate comparisons. By integrating with major eCommerce platforms and providing robust analytics, ShippingEasy helps businesses save time and reduce costs.
7. Easyship
Easyship provides a global logistics solution, integrating over 250 shipping options. Its automated shipping rules refine courier selection based on cost and speed. Easyship also refines customs documentation and offers branded tracking tools. That makes it an excellent choice for businesses looking to expand internationally.
8. Veeqo
Veeqo is a free shipping management platform that integrates with major carriers to provide immediate rate discounts. Its features include bulk shipping, automated rules based on order specifications, and real-time tracking. As part of the Amazon family, Veeqo also ensures data security and convenient platform compatibility, making it a reliable tool for shipping automation.
9. ShipHero
ShipHero combines warehouse management with automated shipping capabilities. Its features include batch picking, live checkout rates, and efficient route calculation. ShipHero’s AI-powered smart package assignment improves shipping processes. It leads to reduced errors and better customer satisfaction.
10. SendCloud
SendCloud is a Europe-based platform that automates shipping processes for over 23,000 businesses. Its tools include label printing, smart shipping rules, and automated returns management. With support for regional and international carriers, SendCloud enriches the shipping experience for both businesses and customers.
Benefits of Shipping Automation
Shipping automation is revolutionizing how businesses manage their logistics, bringing precision, efficiency, and customer satisfaction to the forefront.
Below, we explain the key benefits of adopting automated shipping solutions.
1. Enhanced Operational Efficiency
Automated shipping systems simplify complex logistics workflows, from order processing to delivery management. By automating repetitive tasks like label generation, carrier selection, and shipment tracking, businesses can focus on strategic growth rather than manual labor. These systems handle high volumes of orders without bottlenecks, ensuring timely deliveries.
Consider a business experiencing seasonal sales spikes. With automation, they can handle a sudden influx of orders without hiring additional staff. For example, during the holiday season, an automated system can manage bulk shipments, reduce errors, and ensure accurate deliveries, keeping both customers and teams satisfied.
2. Minimized Human Error
Manual shipping processes are prone to mistakes such as incorrect address entry or mismatched orders. These mistakes can lead to customer dissatisfaction and increased costs. Automation technology eliminates these human errors by standardizing processes and ensuring accuracy at every step.
For instance, an automated system cross-verifies order details against customer inputs before generating labels. This eliminates common issues like incorrect packaging or misrouted shipments and saves businesses from costly rectifications.
3. Live Tracking and Monitoring
Real-time package tracking provides businesses and customers with complete visibility over shipments. Automated systems integrate GPS and advanced tracking tools to offer live updates, ensuring accountability and transparency.
Imagine a customer eagerly awaiting their parcel. With live tracking, they can monitor the delivery's progress, reducing anxiety and building trust. Businesses, on the other hand, can use this data to address delivery delays proactively, enhancing operational control.
4. Faster Order Fulfillment
Automation accelerates every stage of the shipping process, from order placement to final delivery. By integrating with e-commerce platforms, these systems ensure orders are processed and dispatched swiftly, meeting the expectations of today’s fast-paced consumers.
For example, an online retailer promising same-day delivery can rely on automation for picking and packing. They can get their packing slips, avoid manual handling, and ship products within hours. This speed not only improves customer satisfaction but also fosters repeat purchases and leads to reduced labor expenses.
5. Cost Savings
Automating shipping reduces human intervention, minimizes errors, and upgrades carrier selection. As a result, it leads to significant cost savings while maintaining consistent quality. Businesses can allocate resources more efficiently, ensuring long-term profitability.
Consider a mid-sized e-commerce business that automates carrier comparisons to choose the most cost-effective option for each shipment. It leads to lower costs, a lesser human workforce, and consistent delivery quality, giving the business a competitive edge.
6. Enhanced Customer Experience
Shipping automation technology creates a hassle-free and fast shipping experience for customers by ensuring accurate deliveries, real-time updates, and faster order processing. Satisfied customers are more likely to leave positive reviews and become repeat buyers.
For instance, a customer receiving timely updates and accurate delivery predictions feels valued. This trust translates into brand loyalty, driving long-term customer retention and positive word-of-mouth.
7. Growth-Ready Scalability
Automation systems can scale alongside business growth, accommodating increased order volumes and expanding operations without additional complexity. This flexibility is particularly beneficial for businesses with fluctuating seasonal demands. It also gives businesses a significant competitive advantage.
Take a clothing brand launching a new collection. Automation systems allow the business to handle a surge in orders seamlessly, ensuring smooth operations without overburdening existing resources.
8. Sustainability
Shipping automation supports eco-friendly practices by optimizing delivery routes, reducing fuel consumption, and minimizing packaging waste. These sustainability efforts align with modern consumer preferences for environmentally responsible brands.
For example, an automated system calculates the shortest delivery route, reducing emissions while lowering operational costs. Businesses can also use data insights to adopt reusable or minimal packaging, further contributing to sustainability.
How Can ClickPost Help in Shipping Automation?
Simplify your logistics with ClickPost – a comprehensive automated shipping solution designed to transform your operations. From real-time tracking to multi-carrier integration, ClickPost empowers businesses to scale efficiently and optimize operations.
Start automating your shipping processes today and unlock unmatched growth potential!
Conclusion
Automated shipping is a strategic necessity in today’s competitive marketplace. By integrating automation into logistics, businesses can achieve unparalleled efficiency, cost-effectiveness, and customer satisfaction. As technology continues to evolve, the potential for shipping automation will only grow. Businesses that adopt these solutions now position themselves for sustainable growth and operational excellence, redefining logistics for the future.
FAQ's
1. How can shipping automation improve delivery speed and accuracy?
Shipping automation reduces manual intervention by streamlining processes like label generation, order routing, and carrier selection. It ensures faster order processing and fewer errors, leading to timely and precise deliveries.
2. Is shipping automation suitable for small businesses?
Yes, shipping automation is scalable and can be tailored to suit small businesses. It reduces operational costs, improves efficiency, and supports growth, making it an excellent investment for businesses of all sizes.
3. How does shipping automation reduce shipping costs?
Automation identifies cost-effective carriers, eliminates manual errors, and optimizes delivery routes. These factors collectively lower operational expenses, helping businesses save on logistics without compromising service quality.
4. What difficulties arise in the e-commerce shipping process?
E-commerce shipping challenges include delayed deliveries, lost packages, high operational costs, and inefficiencies in order tracking. Automation addresses these issues by providing real-time visibility, streamlined workflows, and predictive insights.
5. How do I integrate shipping automation into my eCommerce platform?
Shipping automation integrates through APIs or built-in plugins that connect your eCommerce platform to automated shipping software. It enables easy syncing of orders, inventory, and shipping tasks, ensuring a unified logistics experience.